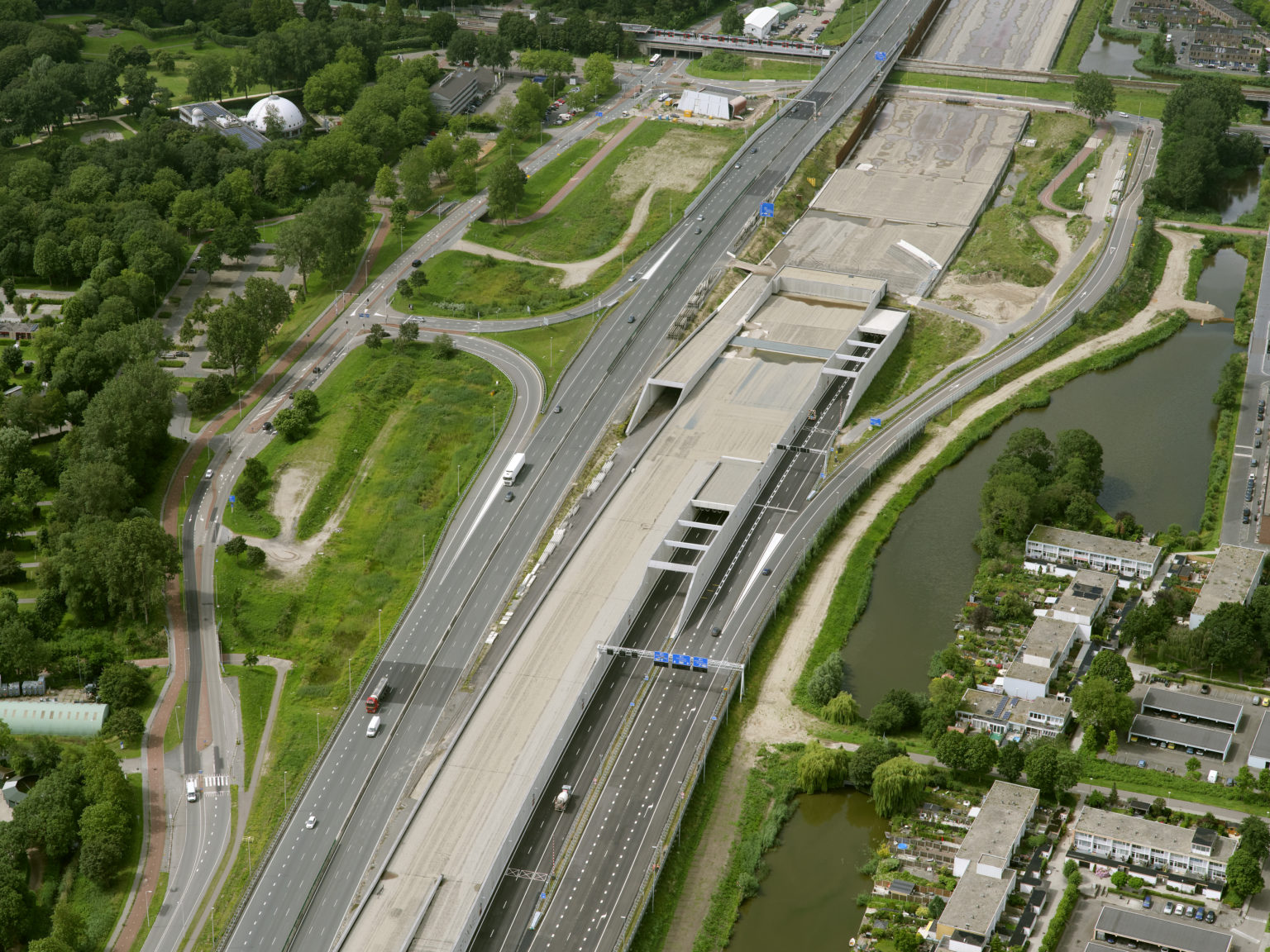
Flexible SCADA platform for civil engineering objects
Automation challenges
The automation challenges that government organizaions are facing when it comes to civil engineering can be characterized as follows:
- the solutions offered must demonstrably comply with the national standards, such as the National Tunnel Standard (Landelijke Tunnelstandaard, LTS) and the National Bridge and Lock Standard (Landelijke Bruggen- en Sluizenstandaard, LBS);
- there is a high degree of diversity in technical systems;
- solutions must facilitate centralized operation (traffic control centers);
- solutions must support a long life cycle (maintenance and evolution).
TNL has developed a flexible SCADA (Supervisory Control and Data Acquisition) platform that is specifically designed to meet these challenges.
Implemented in tunnels
TNL’s SCADA platform has currently been implemented in two different tunnels. The first implementation is in the Gaasperdammertunnel, which opened in the summer of 2020. The other is in the Maasdelta- en Hollandtunnel, an important section of the Blankenburg link (Blankenburgverbinding). This is still under construction, but the development of the technological installation in the tunnel is currently at an advanced stage.
SCADA-platform
The SCADA platform consists of three different functional system parts:
- a graphical user interface (GUI);
- a coordinative control layer;
- a data recorder.
By uncoupling the GUI, the coordinative control layer and the local intelligence, the platform follows the architectural structure contained in the national standards for civil engineering objects (LTS, LBS), see
Figure 1.
The data recorder records all events in the entire system and is an important reference in case of incidents. The data recorder is fitted with extensive search options in an intuitive user interface. This system is also a good basis for asset performance monitoring of all technical elements.

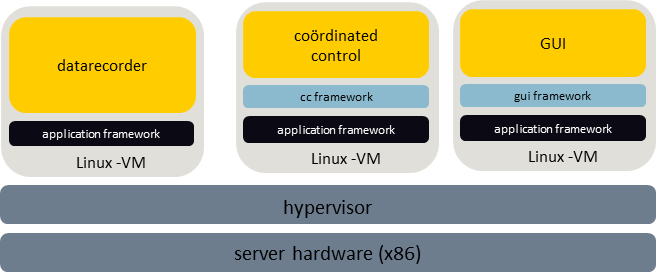
Regular technology
The system parts of the SCADA platform have been built using regular technology. The server systems are normal x86 systems equipped with a hypervisor to create virtual machines. The operating systems used are Linux variants. All applications have been realized in Java. Figure 2 summarizes the structure of the platform.
Flexibility due to separation between technology and logic
The SCADA platform has been built according to a modular architecture, in which logical connections between the various partial systems have been defined. This ensures that the logical functioning of the system is separated from the technical content of the various modules. This makes it possible to change the underlying technology without affecting the integral functioning of the system. If a technical installation is changed or replaced, all that needs to be done is adjust the technical adapter that translates between the logical interface of the installation and the SCADA platform. The functional processing on the user’s side is unaffected.
Demonstrability of requirements
It is crucial for Rijkswaterstaat that automation systems for civil engineering objects comply demonstrably with the requirements set. The SCADA platform has been designed to ensure that the demonstrability and repeatability of requirements are fully integrated. References to relevant requirements have been included in the source code and in the automated test suite. This embedded tracing concept prevents lengthy acceptation processes, because the test status remains complete and up to date throughout the development of the system.
Incremental realization and isolated replacement
The SCADA platform has been designed to separate generic and specific functionality. The generic functionality can be regarded as a ‘container’ that supplies facilities to the substantive functions, making it easier to realize these. This means that, when realizing automation for a particular civil engineering object, normally speaking all that needs to be built are specific logical functions.
The logical functions are realized in such a way as to keep mutual dependence to a minimum. This makes it possible to build the total system in various iterations, with each iteration realizing one or more functional chains. Thus, integration with the various other systems can be effected at an early stage. This prevents heavy, ‘big bang’ integration processes at the end of the project. Figure 3 represents this symbolically by assigning the same colours and numbers to the vertical functional chains. This characteristic also makes it possible to efficiently adapt individual functional chains during necessary renovations. Closure of the objects in question can thus be minimized.
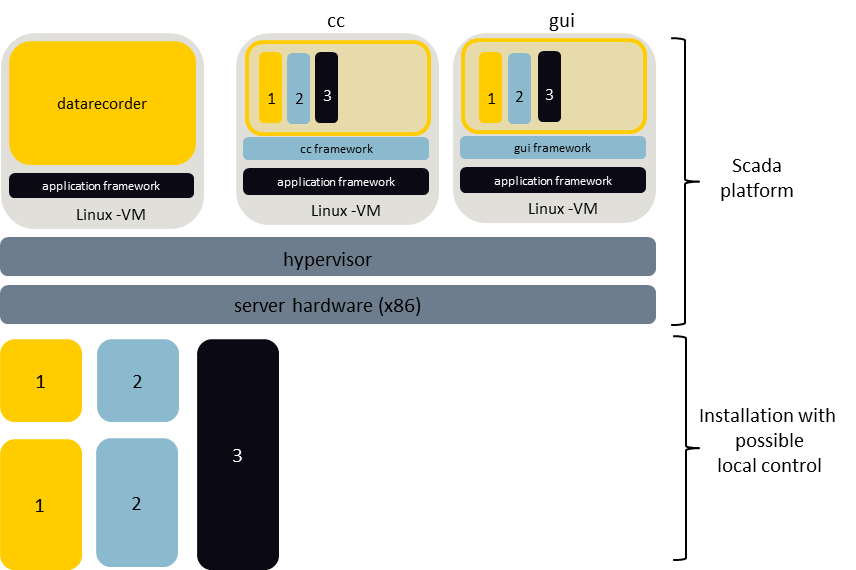
Educational and training system
When a new or upgraded object is commissioned, it is important that staff receives training on how to operate it. This is why, as a matter of course, we include an educational and training mode in the release of every specific platform for a civil engineering object. This mode is equipped with simulators and customized training scenarios. Moreover, the SCADA platform can be connected to a digital representation of the tunnel, which makes it possible to reenact realistic incidents.
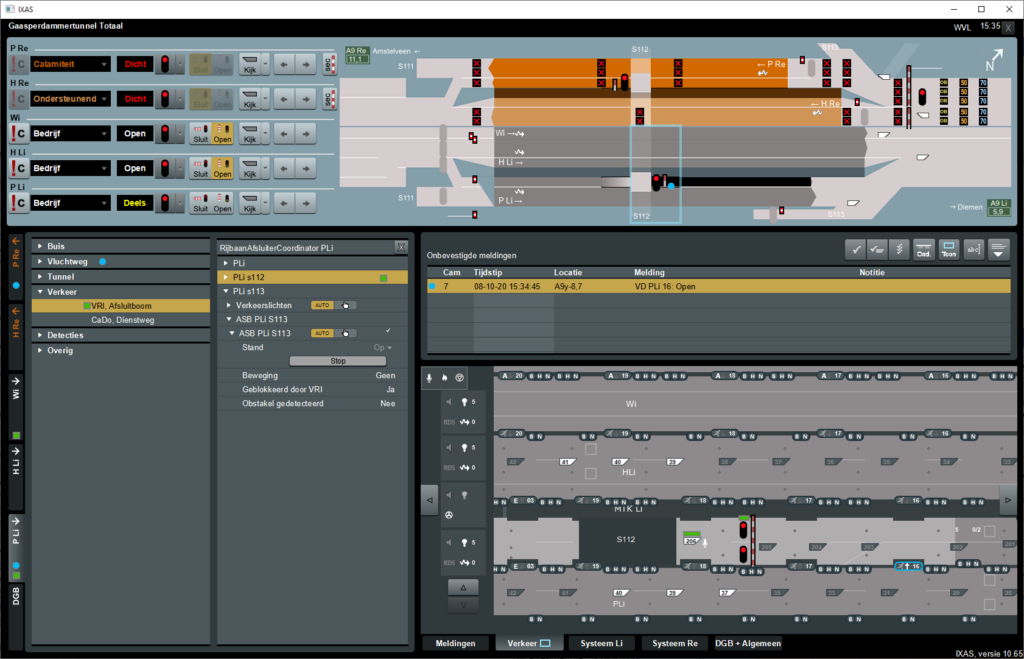
Life cycle and evolution
The automation functions for the objects must be guaranteed for twenty to thirty years. That is a long period, for which a clear replacement strategy is required. By using regular technology in the platform the problem of obsolescence is reduced to a minimum, because the required technology can be supplied by many parties.
It is to be expected that improved technologies for the various subsystems will become available over the coming twenty to thirty years, or that the security requirements for the objects will become stricter. The architectural design that we have chosen makes it possible to renew specific functions separately, without affecting the rest of the system.
The trend in which functionality is increasingly moved to central hosting (‘cloudification’) will also begin to apply to civil engineering objects. With our SCADA platform, you are fully prepared for this. Thanks to the regular technology it uses, the platform does not need to be hosted locally on the site of the object, but can be hosted at any desired location.
Related solutions and projects
Let’s talk about your project
and find out how we can help you
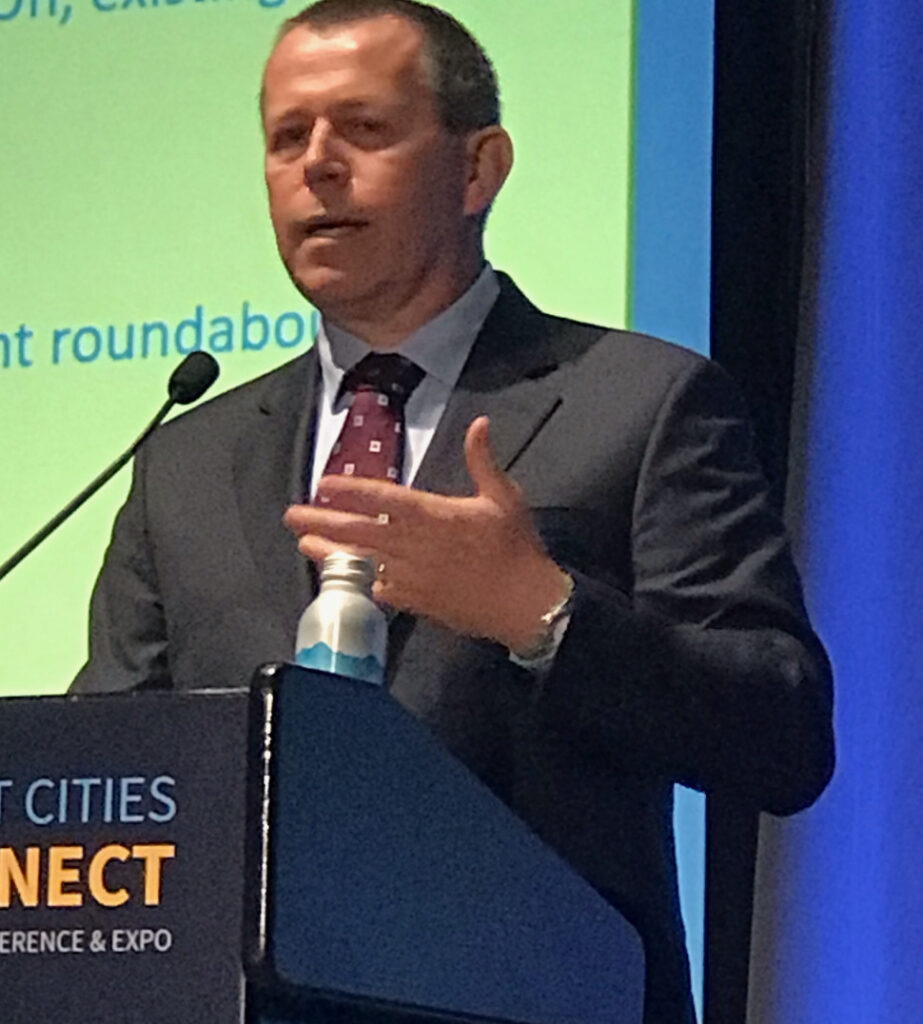